A. Contact loosening back to cracking
Contact is a relay to complete the electrical contact parts to switch the load, some products are riveted contacts with the pressure, the main drawback is the contact is loose, contact cracking or size position deviation is too large. This will affect the contact reliability of the relay. Flooding eradication point loosening, is the reed and contact with the contact department size is not fair or manipulator of the riveting pressure adjustment improperly caused by. Contact cracking is caused by the material hardness too high or too much pressure. For different materials of contacts using different materials process, some hardness of the contact material should be annealed, in the contact manufacturing, riveting or spot welding. Contact manufacturing should be careful, because the material has tolerances exist, so each blocking length should be decided after test touch. Contact manufacturing should not be flooded with flying edge, pad injury and not full phenomenon. Contact riveting deviation is the manipulator will touch the tool is not accurate, the upper and lower touch has a misalignment caused. Contact damage, pollution, is not clean up the touch tool on the oil pollution and iron filings and other things caused. No matter what kind of malpractice, will affect the working reliability of the relay. Therefore, in the contact manufacturing, riveting or welding process, to comply with the first piece of inspection middle sampling and ultimate inspection of self-inspection delineation, to improve the quality of assembly.
Second, the relay parameters are not unstable
Electromagnetic relay parts are riveted with a proportion of the department, the main problem is the riveted loose or poor bonding strength. This fault will make the relay parameters are not unstable, high and low temperature parameter changes, resistance to mechanical vibration, poor impact resistance. The main reason for this fault is that the riveted parts are super poor, improper placement of parts, work touch tool quality disagreement or incorrect installation. Therefore, before riveting and welding to carefully overhaul the tool and riveted parts to meet the requirements.
Third, the electromagnetic system riveted parts deformation
After riveting parts bending, twisting, pier thick black to the next process of assembly or adjustment caused by the problem, and even cause scrap. The reason for this problem is mainly riveted parts are too long, too short or riveting force is not average, touch the assembly deviation or design size error, improper placement of parts caused. In the riveting, manipulation workers should first check the size of the parts, appearance, touch tool is correct, if the touch tool is not in place will affect the quality of the assembly of electromagnetic systems or core deformation, pier coarse.
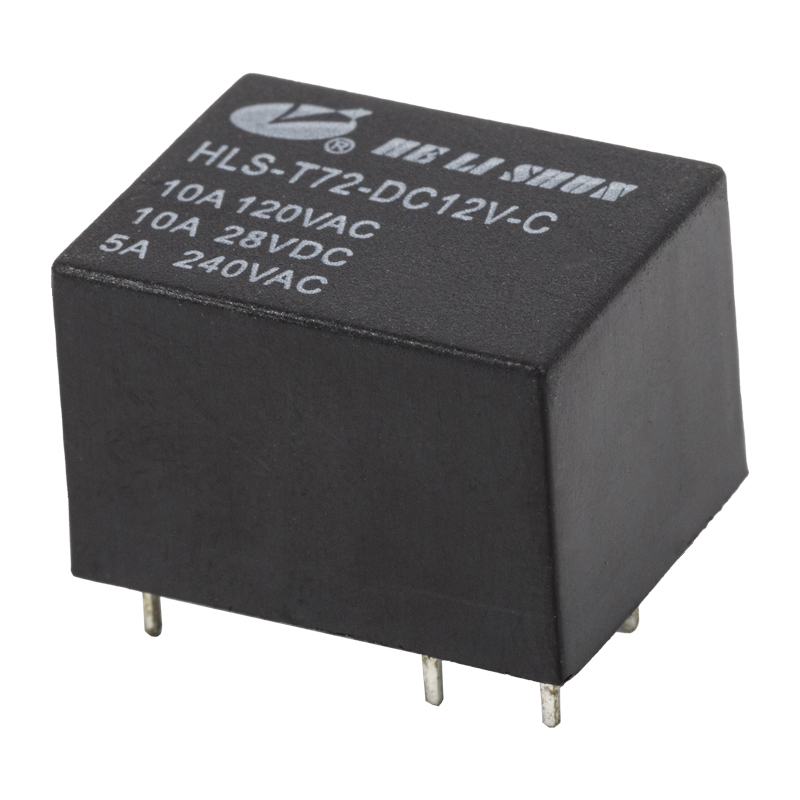
Fourth, the glass insulator damage
Glass insulators are made of metal pins and glass sintered, in the inspection, assembly, adjustment, transportation, cleaning, easy to bend the pins, glass insulators off the block, cracking, and cause gas leakage and when the insulation and voltage resistance SPDT 5PIN 10A power relay PCB PIN HLS-T72 function decreases, pins rolling will cause contact reed displacement, affecting the product reliable through and through. This requires the assembly of the manipulator in the entire process of relay production should be light, parts should be neatly arranged in the transfer box, assembly or adjustment, do not promise to wrench or twist the lead foot.
Five, coil failure
Relays with a wide range of coils, with outsourcing, and without outsourcing, coils should be placed in a single piece separated in a special appliance, if the collision cross-connected, in the separation will cause a broken line. In the electromagnetic system riveting, hand press and press pressure adjustment should be moderate, too much pressure will cause coil breakage or coil frame cracking, deformation, winding breakdown. Too little pressure will cause the winding loosening, magnetic loss increases. Multi-winding coils are generally made with different colors of leads for the head. When welding, should pay attention to distinguish, otherwise it will cause the wrong coil welding. Coils with beginning and end requirements are generally marked with a marking method to indicate the beginning and end. When assembling and welding, attention should be paid, otherwise it will cause the opposite of the relay level.